خانه / دسته بندی محصولات / ماشین آلات / خط تولید / خط تولید گریس / دستگاه تولید گریس
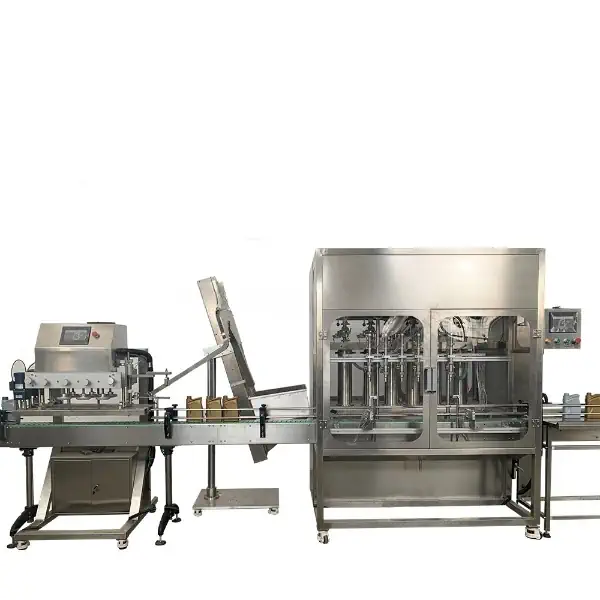
دستگاه تولید گریس
5 / 5.0
براساس 0 نظر مشتریان
توضیحات
اجزای اصلی دستگاههای تولید گریس
یک دستگاه تولید گریس معمولاً از چندین بخش متصل به هم تشکیل شده است که هر کدام نقش خاصی در اطمینان از ترکیب یکنواخت روغن، غلیظکننده و افزودنیها به عهده دارند.
1. میکسر یا آگیتور پرسرعت
میکسر قلب فرآیند تولید گریس محسوب میشود. این بخش مسئول ترکیب دقیق روغن پایه با غلیظکنندهها و افزودنیها است. میکسر پرسرعت در شرایط کنترلشده عمل میکند تا مواد به صورت همگن ترکیب شوند. طراحی صحیح میکسر اهمیت ویژهای دارد؛ زیرا اختلال در مخلوطسازی میتواند منجر به ناهماهنگی در ویژگیهای نهایی گریس مانند ویسکوزیته، پایداری و عملکرد در شرایط مختلف عملیاتی شود.
2. راکتور یا محفظه حرارتی
راکتور جایی است که در آن فرآیند اولیه ترکیب مواد صورت میگیرد. این بخش با داشتن سیستمهای حرارتی، دمای لازم برای فعالسازی غلیظکنندهها و اطمینان از توزیع یکنواخت آنها در روغن را فراهم میکند. کنترل دقیق دما در این مرحله حیاتی است؛ چرا که تغییرات ناخواسته میتواند باعث واکنشهای ناقص یا تخریب افزودنیها شود. راکتورهای مدرن معمولاً شامل سیستمهای اتوماسیون با حسگرهای دقیق هستند که بهطور پیوسته فرآیند را کنترل میکنند.
3. پمپها و سیستمهای انتقال مواد
در طول فرآیند تولید، نیاز به انتقال مواد از یک مرحله به مرحله دیگر وجود دارد. پمپها و سیستمهای انتقال به جابجایی ترکیب از راکتور به بخشهای خنکسازی یا نهایی کمک میکنند. این سیستمها به گونهای طراحی شدهاند که بدون ایجاد جدایی یا ورود هوا به مخلوط، بتوانند مواد با ویسکوزیته بالا را به طور یکنواخت انتقال دهند.
4. سیستمهای خنککننده
پس از پایان واکنش شیمیایی و ترکیب اولیه، مخلوط داغ باید به صورت کنترلشده خنک شود تا گریس به شکل نیمهجامد درآید. سیستمهای خنککننده که ممکن است شامل مبدلهای حرارتی یا کولرهای صنعتی باشند، اطمینان حاصل میکنند که محصول به دمای مطلوب رسیده و ساختار شیمیایی آن حفظ شود. خنکسازی سریع اما کنترلشده برای تثبیت ویژگیهای گریس، مانند نقطه ذوب و مقاومت در برابر تغییرات دمایی، ضروری است.
5. سیستمهای کنترل و اتوماسیون
دستگاههای تولید گریس مدرن مجهز به سیستمهای کنترل پیشرفتهای هستند که پارامترهایی مانند دما، سرعت مخلوطسازی و جریان مواد را نظارت میکنند. این سیستمهای اتوماسیون با استفاده از حلقههای بازخورد خودکار، در صورت انحراف از پارامترهای تنظیمشده، به سرعت اصلاحات لازم را اعمال میکنند تا از یکنواختی محصول اطمینان حاصل شود. استفاده از کنترلرهای منطقی برنامهپذیر (PLC) و رابطهای کاربر-ماشین (HMI) باعث شده است تا تولید گریس به فرآیندی دقیق، کارآمد و قابل پیشبینی تبدیل شود.
6. واحدهای دوزینگ افزودنی
برای تولید گریسهای با ویژگیهای عملکردی ویژه، افزودنیهای خاص باید در غلظتهای دقیق وارد ترکیب شوند. واحدهای دوزینگ مخصوص، این امکان را فراهم میکنند که حتی مقادیر بسیار اندکی از افزودنیها بهطور دقیق در مراحل مناسب تولید اضافه شوند. دقت در دوزینگ از اهمیت ویژهای برخوردار است، زیرا عملکرد گریس در شرایط بارگذاری بالا به ترکیب دقیق این مواد وابسته است.
فرآیند تولید گریس
تولید گریس شامل چندین مرحله کلیدی است که هر یک نیاز به کنترل و نظارت دقیق دارند:
مرحله 1: پیشپردازش و آمادهسازی مواد
پیش از شروع تولید، مواد اولیه شامل روغن پایه، غلیظکنندهها و افزودنیها اندازهگیری و آماده میشوند. کیفیت مواد اولیه بسیار حیاتی است؛ زیرا هر گونه ناخالصی یا نسبت نامناسب میتواند باعث نقص در محصول نهایی شود. این مواد معمولاً در مخازن مخصوص نگهداری شده و در صورت نیاز پیشگرم میشوند تا دمای یکنواخت و ترکیب مناسب حاصل شود.
مرحله 2: مخلوطسازی و واکنش
در محفظه واکنش، روغن پایه و غلیظکننده در دمای کنترلشده با استفاده از میکسر پرسرعت مخلوط میشوند. در این مرحله، غلیظکنندهها فعال شده و بهطور یکنواخت در روغن پخش میشوند. در بسیاری از موارد، این مرحله شامل واکنش شیمیایی میشود؛ بهویژه در استفاده از غلیظکنندههای مبتنی بر صابون، که واکنش بین روغن و ترکیبات قلیایی منجر به تشکیل ساختار گریس میشود.
مرحله 3: وارد کردن افزودنیها
پس از اتمام مخلوطسازی اولیه، افزودنیها به ترکیب اضافه میشوند. این افزودنیها میتوانند شامل عوامل ضد سایش، مهارکنندههای زنگزدگی و افزودنیهای مقاوم در برابر فشارهای بالا باشند. دوز دقیق افزودنیها از اهمیت ویژهای برخوردار است؛ چرا که عملکرد گریس در شرایط سخت به ترکیب مناسب این مواد وابسته است. سیستمهای کنترلی دستگاه در این مرحله نقش مهمی در اطمینان از توزیع یکنواخت افزودنیها دارند.
مرحله 4: خنکسازی و جامدسازی
پس از اتمام واکنش و افزودن مواد، مخلوط داغ به صورت کنترلشده خنک میشود تا گریس به حالت نیمهجامد درآید. فرآیند خنکسازی به گونهای طراحی شده که دما به تدریج کاهش یابد و اجازه دهد تا ساختار گریس تثبیت شود. خنکسازی سریع ممکن است منجر به جدایی فازها شود و خنکسازی کند میتواند بر ویسکوزیته و خواص ذوب گریس تأثیر بگذارد.
مرحله 5: کنترل کیفیت و بستهبندی
پس از جامدسازی، گریس تحت آزمایشهای کنترل کیفیت قرار میگیرد. این آزمایشها شامل ارزیابی یکنواختی، ویسکوزیته، نقطه ذوب و مقاومت در برابر دماهای بالا است. تنها پس از گذر از این آزمایشها، محصول به بستهبندی میرسد. سیستمهای بستهبندی خودکار اغلب با دستگاههای تولید همگام شده و فرآیند پرکردن، برچسبزنی و آمادهسازی محصول برای توزیع را به عهده میگیرند.
اهمیت اتوماسیون و کنترل فرآیند
یکی از پیشرفتهای اساسی در فناوری تولید گریس، یکپارچهسازی سیستمهای اتوماسیون است. این سیستمها مزایای زیادی دارند:
- ثبات و قابلیت اطمینان: اتوماسیون تضمین میکند که هر دسته گریس مطابق با استانداردهای سختگیرانه کیفیت تولید شود. حسگرها و کنترلکنندهها بهطور مداوم فرآیند را نظارت کرده و از بروز خطاهای انسانی جلوگیری میکنند.
- افزایش بهرهوری: سیستمهای اتوماسیون میتوانند بهصورت 24 ساعته و 7 روز هفته کار کنند که این موضوع به افزایش توان عملیاتی و کاهش زمان توقف کمک میکند.
- جمعآوری دادهها و قابلیت ردیابی: دستگاههای مدرن تمامی پارامترهای مربوط به تولید را ثبت میکنند. این دادهها برای کنترل کیفیت، عیبیابی و بهبود مستمر فرآیند بسیار ارزشمند هستند.
- صرفهجویی در انرژی: کنترلهای بهینه فرآیند باعث کاهش مصرف انرژی از طریق حفظ شرایط واکنش بهینه و کاهش حرارت ضایعات میشوند.
کاربردها و اهمیت صنعتی
دستگاههای تولید گریس در صنایع متنوعی کاربرد دارند. در زیر به برخی از مهمترین حوزههای صنعتی که به گریسهای با کیفیت بالا نیاز دارند اشاره میکنیم:
1. صنعت خودروسازی
در صنعت خودروسازی، گریس برای روانکاری بلبرینگها، قطعات شاسی و سیستمهای تعلیق استفاده میشود. عملکرد این گریسها تأثیر مستقیمی بر طول عمر و عملکرد وسایل نقلیه دارد. گریسهای با کارایی بالا تضمین میکنند که عملکرد قطعات در شرایط دمایی و بارهای متغیر بهینه باقی بماند.
2. ماشینآلات سنگین و تجهیزات صنعتی
ماشینآلات سنگین در صنایع ساخت و ساز، معدن و تولید، نیازمند روانکنندههایی هستند که بتوانند فشارها و شرایط محیطی سخت را تحمل کنند. گریسهای تولید شده توسط دستگاههای مدرن، مقاومت بالایی در برابر سایش ارائه میدهند که باعث میشود تجهیزات به طور کارآمد و ایمن عمل کنند.
3. صنعت هوافضا
در کاربردهای هوافضا، گریسهایی مورد نیاز هستند که خواص خود را در شرایط دمایی بالا و تغییرات فشار حفظ کنند. دقت دستگاههای تولید گریس در ایجاد محصولات مطابق با استانداردهای سختگیرانه هوافضا، اهمیت ویژهای دارد.
4. صنایع پتروشیمی و شیمیایی
در صنایعی که تجهیزات در معرض شرایط شیمیایی قوی قرار دارند، گریسهای با کیفیت بالا از قطعات متحرک در برابر خوردگی و تخریب شیمیایی محافظت میکنند. دستگاههای تولید گریس این امکان را میدهند که ترکیبات خاصی بر اساس نیازهای صنعتی تدوین و تولید شوند.
5. انرژیهای تجدیدپذیر
تجهیزات مانند توربینهای بادی و سایر نصبهای انرژی تجدیدپذیر نیازمند سیستمهای روانکاری مطمئن هستند تا اصطکاک کاهش یابد و عمر مفید قطعات افزایش یابد. گریسهای مورد استفاده در این حوزه باید پایدار و بلندمدت باشند که اهمیت فناوریهای پیشرفته در تولید آنها را نشان میدهد.
نگهداری و عیبیابی
برای اطمینان از عملکرد بهینه دستگاههای تولید گریس، نگهداری منظم از اهمیت ویژهای برخوردار است. اقدامات نگهداری اصلی عبارتند از:
- کالیبراسیون منظم: حسگرها، میکسرها و واحدهای دوزینگ باید بهطور منظم کالیبره شوند تا دقت فرآیند حفظ شود.
- تمیزکاری و بازرسی: بخشهای مختلف مانند راکتور، میکسرها و خطوط انتقال باید بهصورت دورهای تمیز شوند تا از آلودگی جلوگیری شود. بازرسیهای دورهای نیز به شناسایی سایش و خرابی قطعات متحرک کمک میکنند.
- بهروزرسانی نرمافزاری: سیستمهای اتوماسیون از بهروزرسانیهای نرمافزاری بهرهمند میشوند که عملکرد فرآیند را بهبود بخشیده و ویژگیهای جدیدی را اضافه میکنند.
- نگهداری پیشگیرانه: بازرسیهای دورهای پمپها، سیستمهای خنککننده و پنلهای کنترلی از بروز خرابیهای ناگهانی جلوگیری میکنند و تولید مستمر را تضمین میکنند.
اپراتورها معمولاً برای انجام این اقدامات آموزشی دیدهاند و بسیاری از تأسیسات زمانهایی را برای بازرسیهای کامل برنامهریزی میکنند. نگهداری منظم نه تنها باعث تولید گریس با کیفیت بالا میشود بلکه عمر مفید تجهیزات را نیز افزایش داده و در نهایت منجر به صرفهجویی قابل توجهی در هزینهها میگردد.
روندها و نوآوریهای آینده در تولید گریس
صنعت تولید گریس همواره در حال نوآوری است و چندین روند جدید پیشبینی میشود که آینده این حوزه را شکل خواهند داد:
1. افزایش اتوماسیون و دیجیتالی شدن
ادغام اصول صنعت 4.0 در تولید گریس باعث تحول چشمگیری خواهد شد. با دیجیتالی شدن بیشتر، دستگاهها قادر به تشخیص خودکار خرابی و انجام نگهداری پیشبینانه خواهند بود. تحلیلهای بلادرنگ و یکپارچهسازی دادهها با استفاده از فناوریهای ابری، فرآیند بهینهسازی و تضمین کیفیت محصول را بهبود خواهد بخشید.
2. تولید پایدار
با افزایش تقاضا برای فرآیندهای تولید دوستدار محیط زیست، انتظار میرود که دستگاههای تولید گریس فناوریهایی را بگنجانند که مصرف انرژی را کاهش داده و ضایعات را به حداقل برسانند. همچنین، توسعه روانکنندههای قابل تجزیه زیستی به عنوان یکی از محورهای تحقیقاتی مطرح شده است که تولید روشهای نوین سبز را به دنبال خواهد داشت.
3. سفارشیسازی و انعطافپذیری
نیاز به گریسهای تخصصی، تقاضا برای سیستمهای تولید انعطافپذیر را افزایش داده است. دستگاههای آینده قادر خواهند بود با تغییر سریع فرمولاسیون بدون توقف زیاد، پاسخگوی نیازهای متغیر بازار باشند. این ویژگی امکان سازگاری سریع با روندهای جدید و الزامات صنعتی را فراهم میکند.
4. سیستمهای کنترل کیفیت پیشرفته
پیشرفت در فناوری حسگرها و الگوریتمهای یادگیری ماشین منجر به کنترل دقیقتر فرآیند تولید خواهد شد. سیستمهای کنترل کیفیت پیشرفته قادر خواهند بود به صورت خودکار پارامترها را تنظیم کنند تا هر دسته گریس از استانداردهای دقیق کیفی برخوردار باشد.